Jak optymalnie zaplanować produkcję?
- Opublikowano
- 10 min czytania
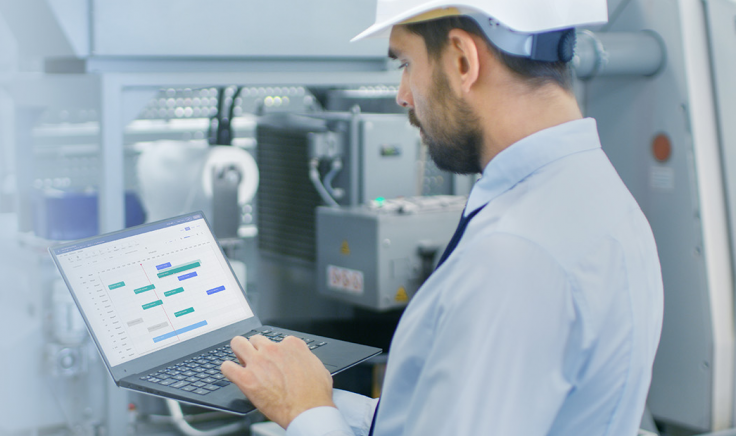
Firmy produkcyjne na co dzień borykają się z wieloma wyzwaniami. Konieczne jest posiadanie odpowiednich materiałów i półproduktów, by realizować produkcję w toku. Klienci wymagają precyzyjnych czasów realizacji oraz dokładnej kalkulacji wyceny produktów. Dodatkowo, aby skutecznie prowadzić produkcję potrzeba wykwalifikowanych pracowników, czy wyspecjalizowanych maszyn, które zapewniają odpowiednią wydajność produkcji.
Wszystkie wskazane obszary łączą się w jedno zagadnienie problemowe, które można zobrazować pytaniem: „jak optymalnie zaplanować produkcję używając dostępnych zasobów, by sprostać wymaganiom Klientów?”.
Planowanie w firmie produkcyjnej - kto bierze w nim udział?
Mimo, że adresatem tego pytania będą wyspecjalizowani pracownicy planistyczni przedsiębiorstwa, to praktycznie każda jednostka organizacji będzie uczestniczyła w procesie uzyskania prawidłowej odpowiedzi:
- Dział sprzedaży przez odpowiednie ustalanie warunków handlowych z Klientem oraz podając realne czasy realizacji;
- Dział technologii przez precyzyjne stworzenie BOM-u (Bill of Materials) oraz technologii produkcji;
- Działy wykonawcze realizując produkcję w założonym czasie i zapewniając odpowiednią jakość wyrobów gotowych;
- Dział kontroli jakości identyfikując z wyprzedzeniem niedoskonałości w produkowanych wyrobach;
- Dział zakupów realizując zapotrzebowanie materiałowe w zaplanowanym czasie;
- Kończąc na pracownikach utrzymania ruchu, którzy muszą zapewnić ciągłość produkcji przez szybką realizację napraw oraz regularne przeglądy maszyn i urządzeń.
Ze względu na powyższe planowanie produkcji jest jednym z najbardziej złożonych i trudnych zagadnień każdego przedsiębiorstwa produkcyjnego. Aby planować skutecznie, planiści muszą posiadać szerokie doświadczenie produkcyjno-technologiczne i znać dokładnie specyfikę produkcji swojego przedsiębiorstwa. Firmy produkcyjne z tej samej branży często mają odmienne podejście do organizacji pracy, gospodarki materiałowej, zarządzania procesem kontroli jakości. Powoduje to, że filozofia planowania produkcji może być inna dla każdego zakładu produkcyjnego. Występują przedsiębiorstwa, które jako główny wyznacznik planowania produkcji wskazują dostępność surowców. Inne skupiają się na wąskich gardłach w produkcji np. obciążenie danej linii produkcyjnej, czy dostępność wyspecjalizowanych pracowników.
Ze względu na różną specyfikę działalności zakładów produkcyjnych możemy wyróżnić cztery podstawowe strategie planowania produkcji:
ETO (Engineer-to-Order), czyli projektowanie pod zamówienia
Ten typ planowania występuje firmach, które dostarczają produkty niepowtarzalne, a projekt jest wykonywany dopiero po otrzymaniu zamówienia od klienta. Wpływa to na znaczne wydłużenie procesu produkcyjnego i czasu realizacji.
MTO (Make-to-Order) inaczej produkcja pod zamówienie
Strategia charakterystyczna dla firm produkcyjnych posiadających różnorodną gamę produktów uzależnioną od zamówień i wymagań konsumentów. Wyroby gotowe są w dużej mierze dedykowane klientom, lecz mogą być wariantami produktu bazowego. Zakup materiałów odbywa się na podstawie zamówienia od klienta lub analiz historycznych zużyć/trendów sprzedażowych. Proces produkcji wymaga dużej tolerancji ze strony klienta ze względu na czas realizacji zamówienia.
ATO (Assemble-to-Order) tzw. Montaż na Zamówienia
Proces produkcyjny opiera się na wykonywaniu najważniejszych podzespołów na zapas i składaniu wyrobu gotowego, gdy wpłynie zamówienie od klienta. Wyroby gotowe najczęściej składają się ze standardowych komponentów, co pozwala na szybką realizację zamówienia. Ze względu na ryzyko pojawienia się komponentów niskorotujących, konieczne jest analizowanie trendów sprzedażowych i historycznego zużycia.
MTS (Make-to-Stock), czyli produkcja na zapas
Ta strategia planowania produkcji jest charakterystyczna, gdy produkty posiadają stały popyt, a klient oczekuje ich dostarczenia w jak najkrótszym czasie. Od przedsiębiorstwa wymagane jest utrzymanie odpowiednich zapasów magazynowych standardowych produktów, jak i jego wariantów. Kluczowe w procesie produkcji jest prognozowanie zapotrzebowania na wyroby gotowe i wychwytywanie towarów niskorotujących.
Niezależnie od strategii planowania produkcji wyróżniamy dwa kluczowe elementy dla tego procesu: plan oraz harmonogram produkcji.
Plan produkcji
Na podstawie planów sprzedaży, aktualnych zamówień oraz umów powstaje zapotrzebowanie na wyroby w określnym okresie czasu. W oparciu o otrzymane zapotrzebowanie, weryfikując jednocześnie aktualne stany magazynowe możemy stworzyć plan produkcji. Dla planu produkcji ustalany jest horyzont planistyczny (zazwyczaj 1 – 3 miesiące), dla którego planista będzie prowadził analizę zapotrzebowania i zdolności wytwórczej zakładu produkcyjnego.
Pod kątem ustalenia zdolności wytwórczej istotna dla planisty jest informacja o dostępnych stanach magazynowych materiałów oraz zasobach produkcyjnych. W tym celu dział technologii powinien utworzyć Technologię Bill of Materials pod dany wyrób, aby planista mógł określić zapotrzebowanie na surowce i półprodukty oraz zestawić je z dostępnymi stanami magazynowymi.
Kolejnym kluczowym elementem jest capacity (zdolność produkcyjna) poszczególnych gniazd roboczych (maszyn i ludzi) w danym horyzoncie czasu. Użytecznym narzędziem dla działów planistycznych w tym przypadku jest możliwość sprawdzenia aktualnego obciążenia gniazd produkcyjnych i wskazanie, jakie są dostępne moce przerobowe. Po dokonaniu odpowiednich kalkulacji przez planistę tworzy on plan produkcji na poszczególne wyroby (najczęściej w układzie tygodniowym).
Hamonogram produkcji
Harmonogram produkcji uszczegóławia plan produkcji w krótkim horyzoncie czasowym (tygodnia, dnia, konkretnej zmiany). Plan produkcji, a dokładnie operacje produkcyjne wynikające z technologii są rozpisywane na poszczególne zmiany, maszyny i zasoby. W harmonogramie produkcji ustalamy w jakiej kolejności poszczególne operacje produkcyjne mają być realizowane na zasobach. W harmonogramowaniu produkcji uwzględniamy również takie elementy jak:
- kompetencje pracowników,
- czasy i koszty przezbrojeń maszyn,
- operacje przygotowawczo-zakończeniowe (np. przygotowanie stanowiska produkcyjnego),
- przerwy między operacjami (np. schnięcie elementu po malowaniu).
Harmonogram produkcji jest następnie kontrolowany pod kątem stopnia realizacji przy pomocy narzędzi do monitorowania produkcji (MES).
Jak optymalizować planowanie i harmonogramowanie produkcji?
Ze względu na to, że planowanie jest ściśle związane z wewnętrznymi procesami produkcji, aby móc je optymalizować wymagane jest wprowadzenie odpowiednich metod optymalizacji zarządzania produkcją. Poniżej przedstawiono kilka z nich:
Mapowanie procesów produkcyjnych
W ramach tej metody tworzona jest dokładna mapa etapów produkcji oraz procesów logistycznych przedsiębiorstwa jako całość. Analizując wskazaną mapę wyszukujemy etapy, które należy usprawnić oraz predefiniujemy powiązania miedzy procesami, by optymalizować przepływy materiałów i pracy.
Kaizen
To optymalizacja produkcji przez wprowadzanie do organizacji sposobu myślenia i idei ciągłego doskonalenia procesu produkcyjnego. Metoda ta zakłada stopniowe wprowadzanie zmian przez poprawę ergonomii stanowisk pracy, wdrażanie pomysłów pochodzących od pracowników operacyjnych i angażowanie ich w proces zwiększenia wydajności firmy oraz redukcję kosztów.
One Piece Flow
Oznacza (“przepływ jednej sztuki w gnieździe”). Wskazana metoda zakłada taką organizację produkcji, by dane komponenty zostały przekazywane ze stanowiska na stanowisko produkcyjne bez przerw i w określonym tempie. Celem takiego działania jest zmniejszenie ilości zapasów, skrócenie czasów realizacji i wyeliminowanie czynności zbędnych.
5S
Rozwinięcie skrótu to Sortowanie, Systematyka, Sprzątanie, Standaryzacja, Samodyscyplina. Metoda zakłada, że każdy z pracowników dba o porządek w miejscu pracy, a narzędzia znajdują się w takich miejscach, by zapewniały ekonomię i ergonomię pracy.
Odpowiednie narzędzie do planowania produkcji
Poza wyborem odpowiedniej metody optymalizacji zarządzania produkcją ważne jest posiadanie odpowiedniego narzędzia do planowania i harmonogramowania produkcji.
Jakie narzędzia może zastosować zakład produkcyjny w obszarze planowania i harmonogramowania produkcji?
Microsoft Excel?
Wiele firm produkcyjnych do planowania i harmonogramowania produkcji stosuje arkusze kalkulacyjne pakietu MS Office. Aplikacja MS Excel w elastyczny sposób pozwala kalkulować zapotrzebowanie oraz planować produkcję o zdefiniowane reguły dostępności/zdolności produkcyjnej.
Ogromną zaletą tego narzędzia jest łatwość dostępu (niska cena, wiele poradników i kursów dostępnych na rynku, niski próg wejścia) oraz duża elastyczność, która umożliwia w odpowiedni sposób przełożenie na arkusz charakterystyki procesów produkcji organizacji. Planowanie i harmonogramowanie produkcji w tym narzędziu ma jednocześnie wiele wad:
- Brak bezpośredniej integracji z innymi systemami IT, które dostarczają informacji o stanach magazynów surowców/półproduktów i zdolnościach produkcyjnych. Od planisty wymagane jest systematyczne importowanie do MS Excel powyższych danych. Nie można jednak tego zrealizować automatycznie podczas procesu planowania, co skutkuje ryzykiem niedokładnych szacunków;
- Utrudniona wymiana informacji między działami uczestniczącymi w procesie planowania produkcji. Plany i harmonogramy produkcji w formie arkuszy MS Excel krążą między różnymi działami, które dopisują do niego istotne informacje. Stwarza to ryzyko posiadania kilku wersji pliku z planem produkcji i braku wiedzy, który jest aktualny oraz wiążący;
- Ryzyko utraty wiedzy o planowaniu i harmonogramowaniu produkcji. Schemat metodologii planowania produkcji zobrazowany w MS Excel jest często indywidualną konstrukcją stworzoną przez planistę. Na pytanie jak powstaje wynik planowania produkcji i jak go interpretować odpowiedź ma tylko planista. W przypadku odejścia takiej osoby z organizacji pozostali pracownicy przedsiębiorstwa nie będą w stanie w odpowiedni sposób pracować na stworzonym arkuszu kalkulacyjnym;
- Czasochłonne dokonywanie ciągłych zmian w arkuszu MS Excel, aby uaktualnić plan produkcji;
- Ograniczenie technologiczne i funkcjonalne. Narzędzie MS Excel ma wiele ograniczeń technologicznych i funkcjonalnych takich jak: brak możliwości porównywania wielu wersji planów, brak automatycznego przeplanowania produkcji, brak zaawansowanych algorytmów harmonogramowania produkcji, brak interaktywnego wykresu Gantta, czy czytelnej wizualizacji konfliktów i zagrożeń na wykresie Gantta;
Systemy klasy ERP
Nowoczesne systemy IT, jak Comarch ERP XL posiadają moduły do planowania produkcji. Dużą zaletą takich systemów jest pełen dostęp do informacji o stanach magazynowych, zasobach produkcyjnych, technologii produkcji (BOM i marszruta). Zintegrowany przepływ informacji pozwala planiście na optymalne utworzenie zapotrzebowania na podstawie planów sprzedaży oraz przeanalizować dostępne stany magazynowe wyrobów gotowych. Następnie po utworzeniu planu produkcji możemy jednocześnie zaplanować zakup materiałów. Plan produkcji w kolejnym kroku zostanie przekształcony w zlecenia produkcyjne, co uruchomi produkcję toku i poinformuje odpowiednie działy wykonawcze.
Systemy klasy ERP wspierają również przedsiębiorstwa w zakresie harmonogramowania produkcji. Przykładowo w Comarch ERP XL planista ma dostęp do funkcji automatycznego planowania i przeplanowania produkcji wg. określonych reguł. Dodatkowo poprzez interaktywny wykres Gantta można przesunąć daną operację w czasie, skrócić/wydłużyć jej czas trwania lub przenieść na inny zasób produkcyjny.
Do wad niniejszej klasy systemów IT należy ograniczona elastyczność tworzenia metod planowania i harmonogramowania produkcji, ze względu na pełną integracje z innymi modułami systemu ERP.
Systemy klasy APS
APS, czyli zaawansowane planowanie i harmonogramowanie (z ang. Advanced planning and scheduling) są to narzędzia IT pozwalające na złożone operacje planistyczne wraz z ich optymalizacją w zakresie procesów produkcyjnych. W odróżnieniu od rozwiązań ERP ta klasa systemów IT skupia się wyłącznie na aspekcie optymalizacji planowania produkcji. W wyniku czego systemy APS charakteryzują się dużą elastycznością dostosowania funkcjonalności do specyfiki procesów produkcyjnych przedsiębiorstwa oraz wysoką wydajnością przetwarzania danych przy harmonogramowaniu i planowaniu. Systemy APS działają w oparciu o zaawansowane algorytmy planistyczne oraz narzędzia do konfiguracji, które optymalizują metody harmonogramowania i organizację produkcji.
Rozwiązania klasy APS są uzupełnieniem systemów ERP i działają niezależnie. Ze względu na to konieczna jest obustronna synchronizacja danych. System APS zaciąga z rozwiązania ERP informacje o zleceniach produkcyjnych, technologii (Bill Of Materials, marszruta), stanach magazynowych. W odwrotną stronę do systemu ERP trafia zoptymalizowany harmonogram produkcji, czyli informacja w jakiej kolejności i na jakich zasobach mają być realizowanie poszczególne zlecenia i operacje produkcyjne. Konieczność wymiany danych wymaga odpowiedniego stopnia integracji APS z systemem ERP, aby ten proces odbywał się automatycznie. W innym wypadku skutkuje to czasochłonnym importem danych oraz ryzykiem przyjęcia nieaktualnych informacji przy planowaniu/harmonogramowaniu produkcji.
Autor tekstu:
![]() | Sebastian Smiatek Absolwent Uniwersytetu Ekonomicznego w Katowicach na wydziale Ekonomii. Od prawie 10 lat związany z branżą IT w zakresie analityki biznesowej, doradztwa w wyborze właściwych narzędzi IT oraz optymalizacji kluczowych procesów biznesowych w przedsiębiorstwach branży produkcyjnej i handlowej. |
Skomentuj
Brak komentarzy